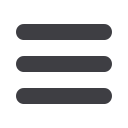
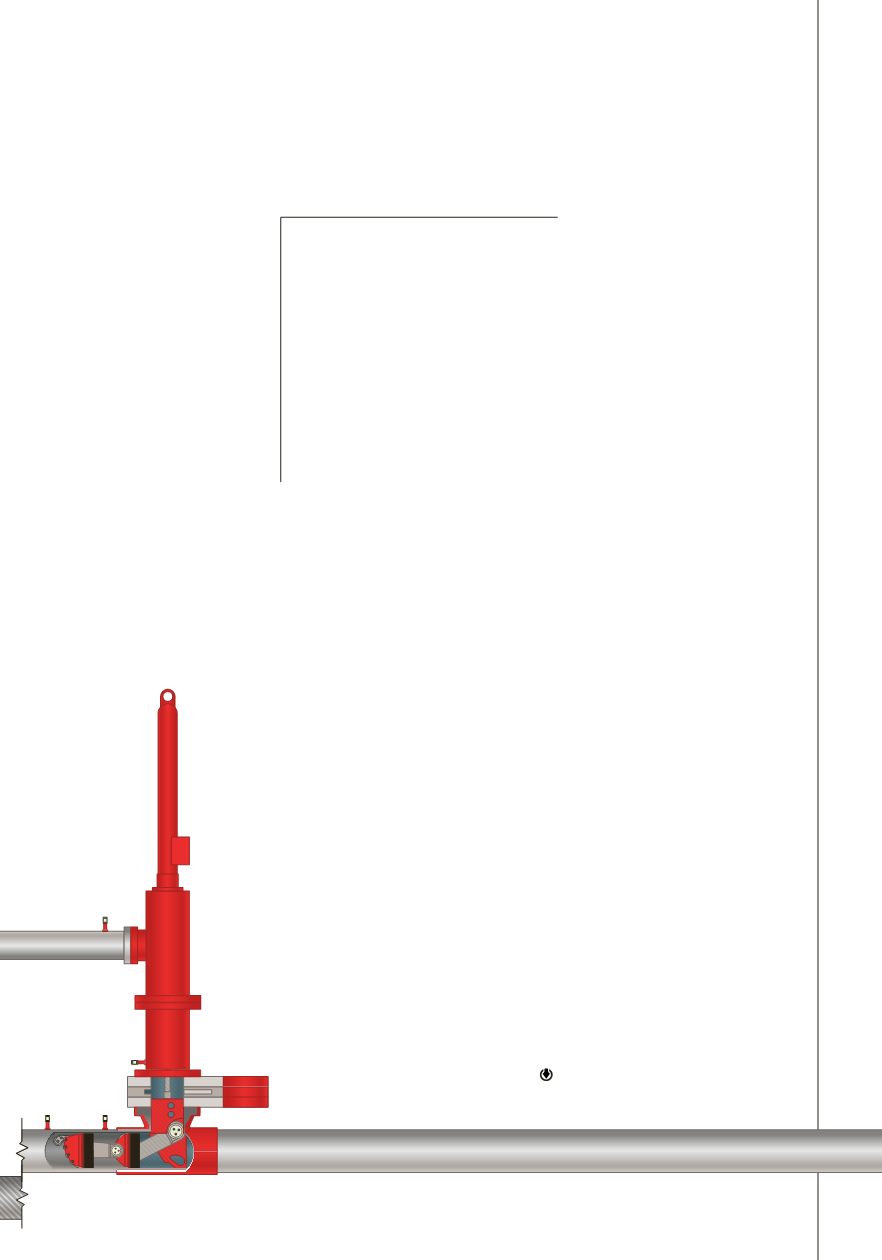
I N N O V AT I O N S • V O L . V I I , N O. 2 • 2 0 1 5
7
By eliminating the
need to bypass flow
through a separate
set of taps, the total
number of fittings is
reduced and the HT&P
process is enhanced.
money. But by eliminating the need to bypass flow
through a separate set of taps, the total number of
fittings is reduced and the
HT&P process is enhanced.
Take for instance a
double isolation bypass
procedure, which is a
common method for
isolating a section of pipe by
sealing it off both upstream
and downstream of the area
that requires work. This
procedure normally requires
two hot taps and two fittings
on each side of the isolation
zone (four fittings total).
One fitting on each side is
used to install the bypass pipe and the other is used
for insertion of the plugging head(s).
Although operators are always looking to
increase the efficiency of their processes, the
current low oil price environment has provided
the industry with renewed determination. This is
where advances in HT&P technology come in.
One such advancement is increased capability
with the patented STOPPLE®
Train plugging system,
developed by T.D.
Williamson (TDW).
Always supported by
specialized applications
engineering, this unique
approach to line isolation
halves the number of
hot taps and fittings by
inserting two independent
seals through a single entry
point, instead of requiring
a tap for each seal. This
isolation method allows
for product bypass directly
through the housing of the
plugging machine.
The STOPPLE
Train system’s two
independent seals, which establish double block
and bleed capability, also provide an extra layer
of safety for the technicians
working on the pipeline and
increase the likelihood of
achieving an acceptable seal on
the first attempt.
“Being able to perform a
double isolation and bypass
through the housing of the
plugging system reduces the
need for additional fittings, and
as any operator who has ever
had to perform an HT&P job
knows, this means significant
cost savings,” explains David
Turner, Director of Hot
Tapping and Plugging Technology at TDW.
“Beyond reducing cost, fewer fittings mean
minimized risk of third-party damage, which is
fairly common. This approach also improves safety
and reduces the size of the excavation required to
get at the pipe, again resulting in lower equipment
costs and less risk for operators,” says Turner.
Simplification Boosts Savings, Too
Simplified field operations are another tangible
benefit of bypassing through the plugging machine
housing. Fewer welds mean reduced manpower
requirements and less time needed to complete the
HT&P operation.
“Any time you can streamline field-related
operations, you’re going to see additional
savings,” says Grant Cooper, Manager of
Commercialization, HT&P Technology for TDW.
“So now, not only have you reduced your number
of fittings by half (i.e., cost and risk), you’ve gained
efficiencies in manpower and time, which translate
into increased safety.”
Finding ways to hedge against fluctuating energy
prices will always be a valuable pursuit for operators.
But in today’s climate, being able to help stabilize
cash flow through more efficient applications of
existing HT&P technology can help yield an even
greater return.