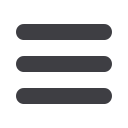
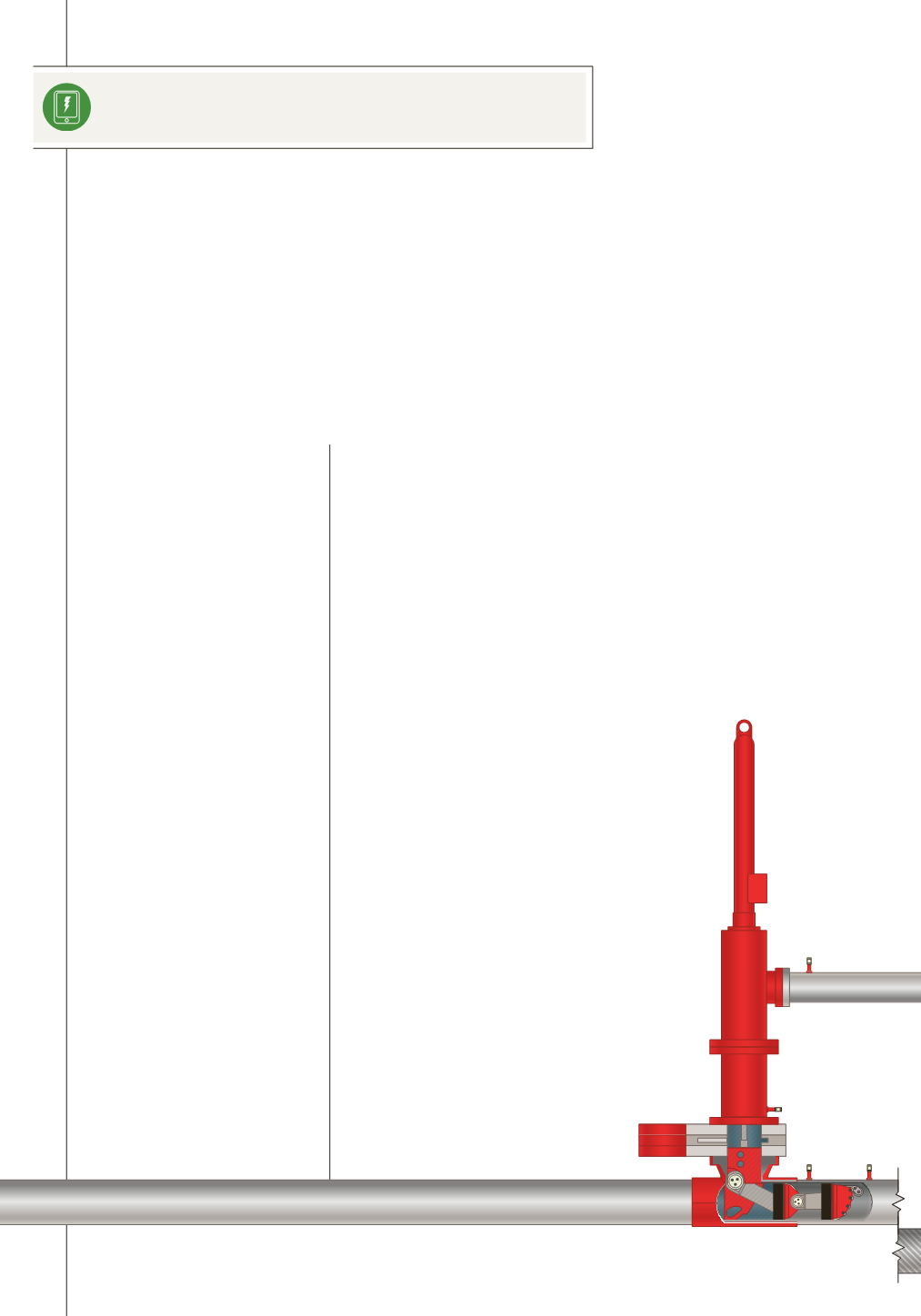
I N N O V AT I O N S • V O L . V I I , N O. 2 • 2 0 1 5
6
T E C H N O L O G Y F O C U S
Tap into Efficiency:
Bypass Pipeline Maintenance Costs
Utilizing the isolation
system housing
to create bypass,
operators achieve major
efficiency gains.
It’s not news that pipelines are a high-maintenance asset.
And for most operators who need to perform maintenance, shutting
their pipeline down simply isn’t an option. Regardless of whether the
product in the line is worth US$100 a barrel or US$40 a barrel, if
flow gets interrupted for any period of time, it’s going to show up on
the P&L statement.
For decades, hot tapping and plugging (HT&P) has been the
preferred method of performing both planned and emergency
maintenance on pipelines. Operators often use HT&P to isolate and
bypass small lengths of pipe so that repairs, modifications, or tie-ins
can be made without having to stop flow and drain or flare product.
This means that, by including a bypass as part of an isolation, operators
can significantly improve their ability to safely
perform maintenance and avoid the financial
pitfalls that accompany shutting down a line.
However, like any technology or
methodology, there’s always opportunity to
realize additional savings by making the process
more efficient. And one way to achieve greater
efficiency is by bypassing flow directly through
the housing of the plugging machine.
Fewer Fittings Mean Lower Costs
Typically, the biggest determinant of cost when
it comes to an HT&P project is how many taps
an operator needs to make in order to isolate
the pipe, bypass flow, and create a safe work
environment for their technicians to perform
maintenance.
More taps means more fittings, more welds,
more potential leak paths, more
inspections, and ultimately, more