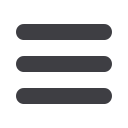
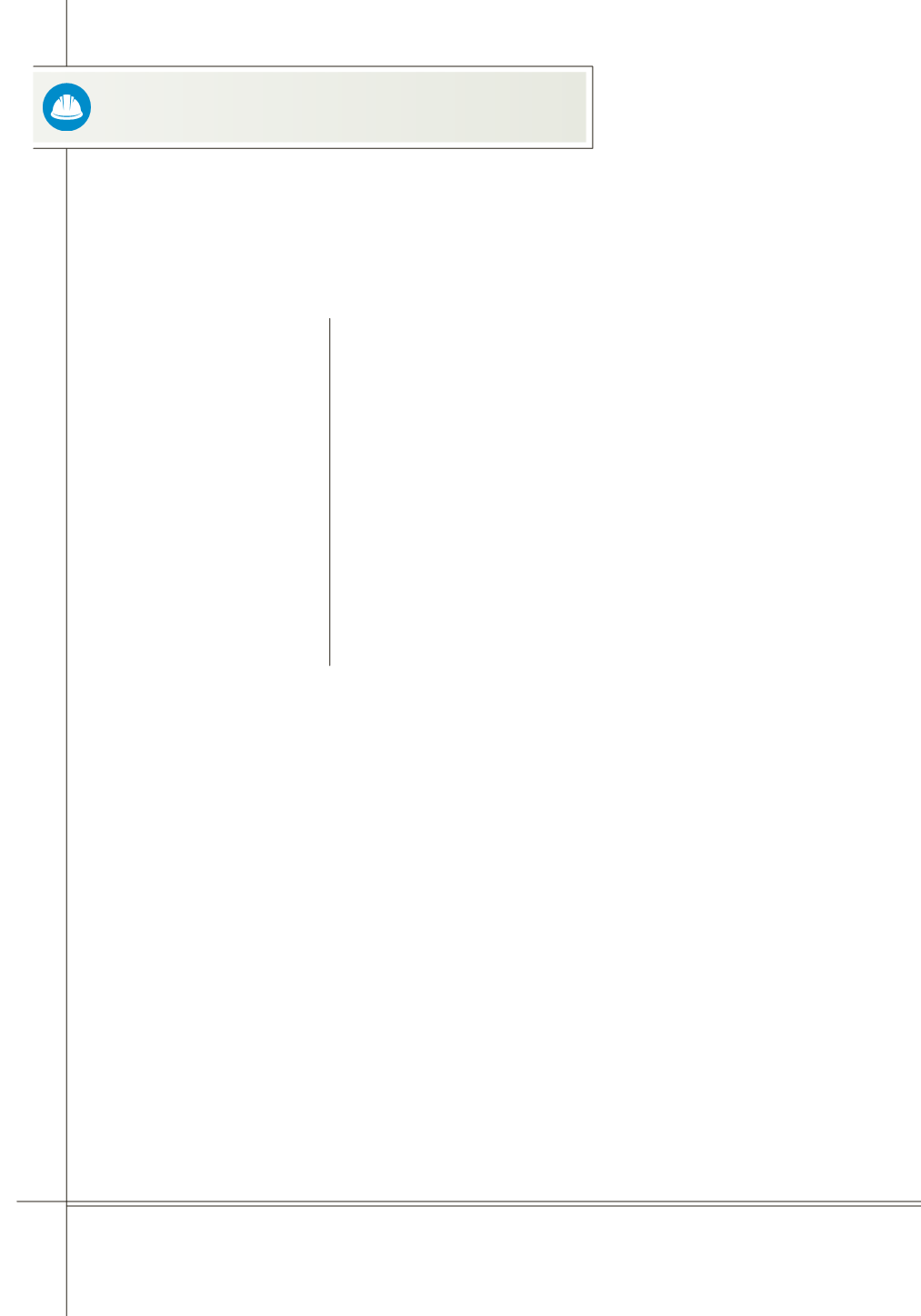
8
I N N O V AT I O N S • V O L . V I I , N O. 2 • 2 0 1 5
Extraordinary
Safety
Measures
for an Everyday Task
On a January day in 1992, residents about 96 kilometers
(60 miles) north of Calgary, Alberta, were forced into the cold,
along with about 600 workers at a gas plant construction camp
site. A pipeline about 800 meters (0.5 miles) a compressor station
ruptured on both sides of a hot tap tee. The natural gas escaping
from the rupture caught fire at three different places along the 373
meters (quarter mile) of damaged pipe. Fortunately, no one was
injured. As reported by the
Oil and Gas Journal
, the primary cause
of the accident was “the noncompliant procedure used to weld the
24- in. stub to the 36-in. carrier pipe.” More specifically, it was faulty
welding that created a hydrogen crack, which, ultimately, couldn’t
handle the stresses from the pipeline.
The accident happened over 20 years ago, but it is still a powerful
illustration of how even everyday procedures like welding require
stringent safety measures and highly specialized professionals to keep
dangerous accidents from occurring on a pipeline.
The Risks of Keeping the Product Flowing
Hydrogen cracking is one of the greatest concerns of pipeline owners.
If hydrogen atoms pool within the steel’s grain boundaries – forming
hydrogen gas – pressure can build and cause cracking. Although the
cracking often becomes apparent just one or two days after welding,
the pipeline can also take up to 10 or more years to show signs.
That’s why hydrogen cracking is often called “delayed cracking.”
Besides hydrogen cracking, the other major danger in pipeline
welding is “burn-through,” which can cause the product inside the
pipeline to leak or even ignite. Burn-through is of significant concern
as almost all pipeline welding is “live welding,” which means that it’s
performed when a pipeline has liquid or gas inside.
Live welding, also known as “in-service welding,” is the first step
in the process for hot tapping and plugging,” says Chris Vrolyk, a
welding engineer manager for T.D. Williamson. This means live
welding is integral to the safe repair and maintenance of pipelines –
such as for tie-ins, defect removal, or making a line piggable. “In fact,
it’s used in most of our services, so we deal with it on a daily basis,”
adds Vrolyk.
Although service companies are well acquainted with the process,
live welding still involves applying concentrated heat on a pipeline
S A F E T Y M AT T E R S
Mitigating the risks of
live welding through
ongoing training.