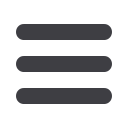
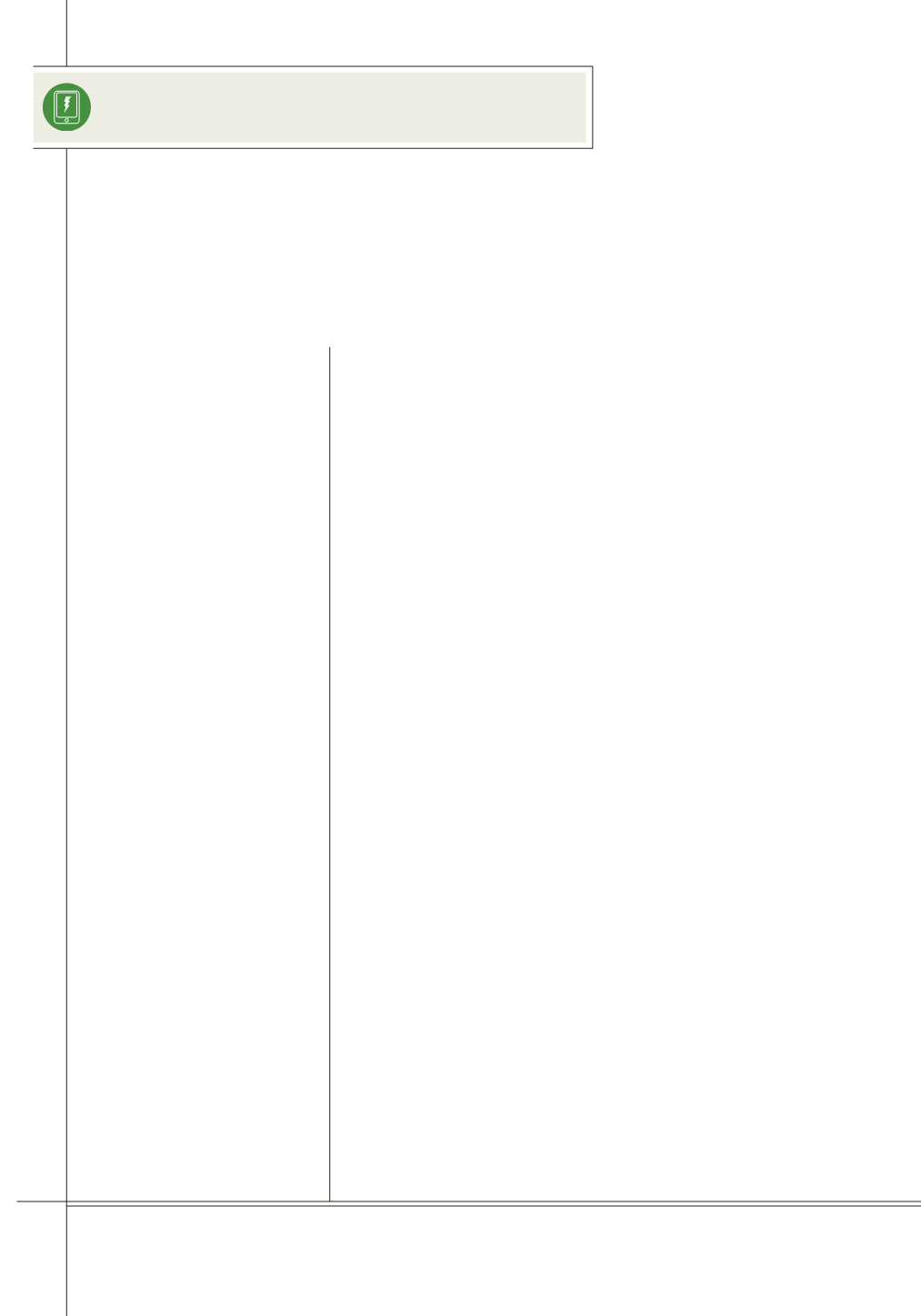
I N N O V AT I O N S • V O L . V I I I , N O. 1 • 2 0 1 6
6
T E C H N O L O G Y F O C U S
Prioritizing in the Pipeline
The year is 1959. Thousands of feet of skelp – plates of
steel – slide through the assembly line, relentlessly pushed, shaped,
twisted into cylinders by back-to-back rotating rolls of gleaming
metal. The emerging modern marvel is whole, except for a gaping long
seam along the entire length. It slides towards two white-hot copper
rings buzzing with current and waiting to receive the soon-to-be-
commissioned pipeline.
It doesn’t take long for the steel to lose the battle. The strip edges fuse
together, finally welding closed, the last bit of light shut out. A shining
testament to pioneering technologies and cutting-edge mechanics.
Except for one thing. The current wasn’t strong – or consistent –
enough. The skelp was run too fast through the welder. The power
fluxed, the skelp was dirty, or the pressure at the bondline was too high
– all causing scores of undetectable flaws.
The same flaws that lie in wait today, over 40 years later.
Underground. In still serviceable pipelines.
The type of pipe is called electric resistance welded (ERW) pipe. In
the early 1900s it was the peak of technology, but as the 21st century
neared, its Achilles’ heel was exposed.
Quick-Spreading and Hard-to-Detect
ERW pipe, along with furnace lap-welded pipe that was
manufactured around the same time period, is especially susceptible
to selective seam weld corrosion (SSWC) – a localized corrosion
attack along the weld bondline that leads to the development of a
rupture-prone wedge-shaped groove.
Although SSWC failures account for less than one percent of
incidents reported, this type of corrosion is of particular concern for
a few reasons: it is traditionally difficult to detect with conventional
inline inspection (ILI) tools, such as axial magnetic flux leakage
(MFL) technologies; SSWC can cause a pipeline to rupture even
under low stress conditions; and selective corrosion grows in service
faster than adjacent pitting corrosion.
It’s no surprise that the Pipeline and Hazardous Materials Safety
Administration (PHMSA) has regulations and standards to ensure
that SSWC is addressed. In fact, PHMSA states that any “corrosion
of or along a longitudinal seam weld” needs to be evaluated and
remediated within 180 days of discovery.
A New Tool in the Fight
Against Selective
Seam Weld Corrosion