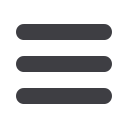
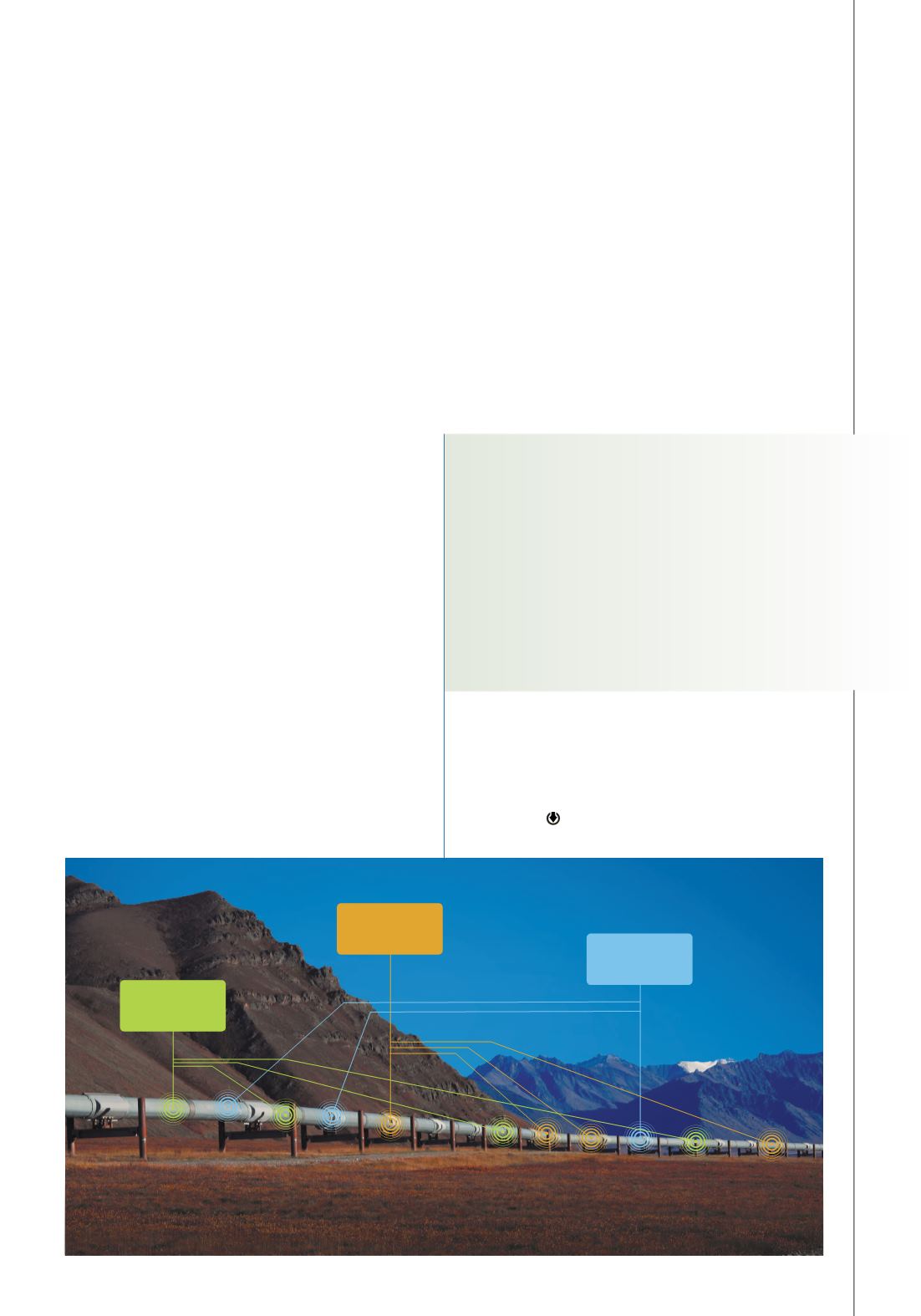
I N N O V AT I O N S • V O L . V I I , N O. 1 • 2 0 1 5
7
BIN 1
BIN 2
BIN 3
MDS can be used to identify common characteristics of a representative sample of pipe joints, producing information
that can be validated by the PMI process and then applied more broadly – saving thousands of miles of joint testing.
“The solution is twofold,” says Chuck Harris,
Commercialization Manager for Pipeline Integrity
Technology at T.D. Williamson (TDW). “First,
inline inspection (ILI) with a comprehensive
technology like the Multiple Dataset Platform, or
MDS, to classify pipe joints by their characteristics.
Second, following the integrity report, verification
of materials through the Positive Materials
Identification (PMI) process.”
As the market’s most comprehensive inspection
platform, MDS is comprised of a robust
combination of complementary technologies.
When specifically applied to IVP requirements,
MDS provides the following:
Low Field Magnetic Flux Leakage (LFM)
,
the foundational dataset for grouping pipe
joints. LFM reveals mechanical characteristics
related to manufacturing and milling through
background gauss levels and microstructure
changes.
Deformation or Geometry inspection (DEF)
,
which identifies bore and long seam trim
characteristics.
High Field Axial Magnetic Flux Leakage
(MFL)
, used to confirm magnetic properties.
SpirALL®MFL
, which distinguishes differences
in long seam characteristics.
Radial/IDOD (internal/external discrimination)
used to identify additional characteristics
related to the internal pipe wall.
In a certain sense, MDS allows operators to go
back in time: The platform can identify carbon steel
pipe joint characteristics based on the manufacturing
or milling process, information that can unlock the
mystery of what a large section or even an entire
pipeline is made of.
As Harris explains, pipe joints with similar
manufacturing or milling should share certain
similar material properties. MDS can be used to
identify common characteristics of a representative
sample of pipe joints, producing information that
can be validated by the PMI process and then
applied more broadly.
“Let’s say MDS has allowed you to identify
1,000 similar joints that are grouped together in
what we’ll call a bin,” Harris says. “It would be
possible, and it’s our objective, to allow a subset of
those 1,000 joints to be validated by PMI and apply
the findings to all 1,000.
“This could then be used as the basis for
identifying material characteristics for all of
the joints in an entire bin. In other words, by
validating a subset of joints, we could determine the
characteristics of all of them,” Harris adds.
The result is the foundation for establishing
complete material records where none exist. And
not only will that fulfill future PHMSA rules, it can
keep operators from looking over their shoulders for
surprises – and maybe stave off a few grey hairs in
the process.