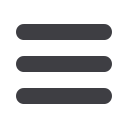
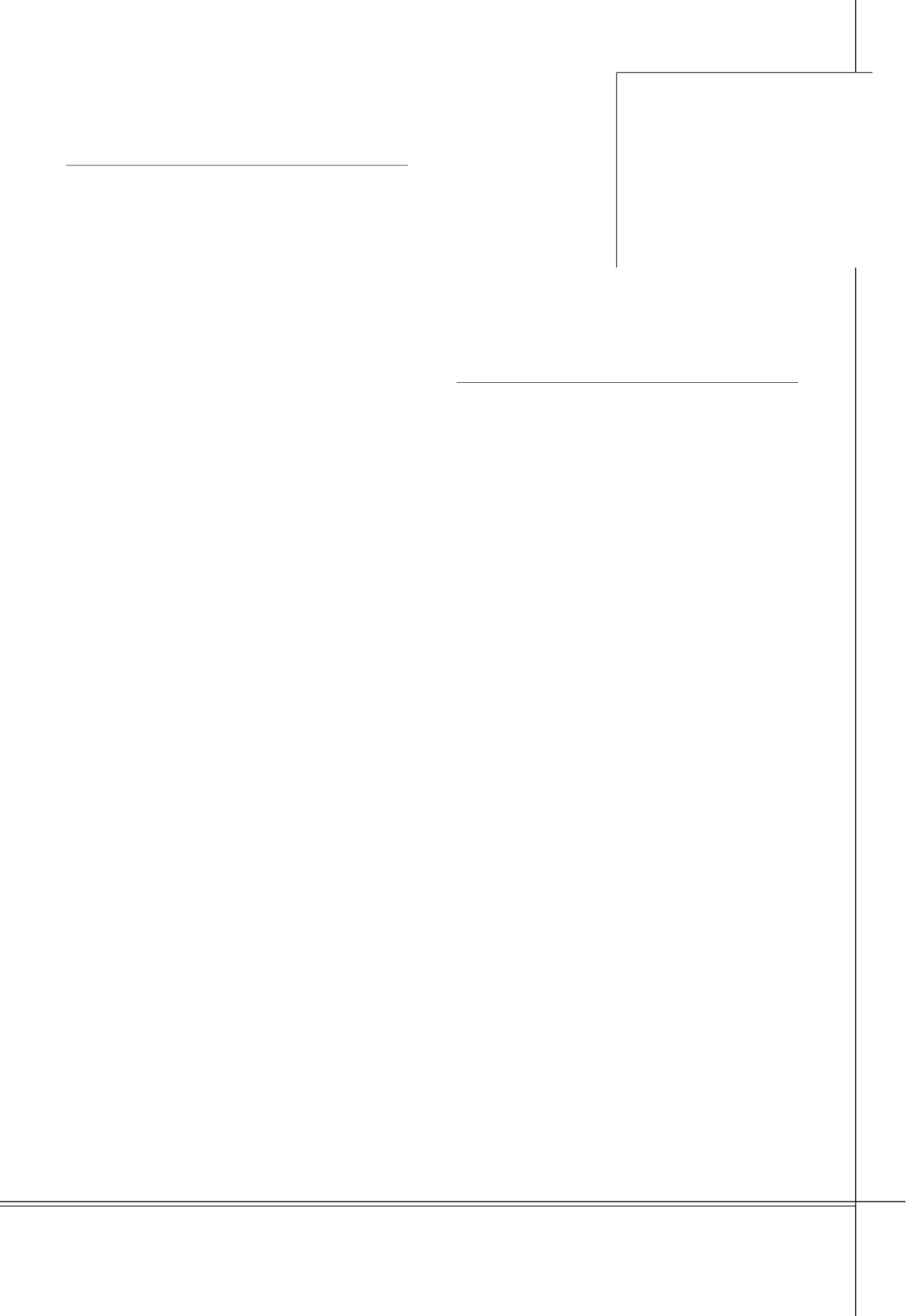
9
I N N O V AT I O N S • V O L . V I I , N O. 1 • 2 0 1 5
SCENARIO 1
DON’T LET SLEEPING BEARS LIE:
INVESTING IN LEGACY EQUIPMENT SAFETY
Legacy pipeline and equipment – hibernating bears
– lead to danger when out of sight becomes out of
mind. And yet, these “bears” may be the trickiest
to contend with because it’s sometimes hard to
convince companies to invest time and capital in
safety upgrades if there haven’t been any incidents.
Say you have a section of pipe that’s been in
operation since the 1970s. Back when it was laid, the
technology was state-of-the-art. But over the years,
perhaps priorities shifted and new projects took
precedence: Companies merge and expand. Records
aren’t always updated. Perhaps, when production
increased, some scheduled maintenance was
overlooked, or postponed – and there’s never been a
problem ... so far.
But then one day, while one of your crew is
performing some routine troubleshooting, that
1970s-era pipeline suddenly suffers a failure. He
winds up in the hospital with life-threatening
injuries, and the impact to the local environment is
substantial.
So, What Should You Have Done?
Kept Up With The Times.
Hollis says there is a lot of advanced safety
technology being deployed within the industry.
For example, T.D. Williamson introduced its
patented double block and bleed STOPPLE®
Train isolation system. This technology effectively
puts additional layers of protection between the
pressurized contents of the line and the personnel
performing repairs or maintenance.
“We’re trying to shift the industry [toward these
kinds of upgrades],” Hollis says. “But while some
companies have adopted this new standard, others
say, ‘Well, we’ve been successful with what we have.
The risk is minimal, so why spend the money?’”
People operate under the assumption that if
there hasn’t been an accident, their equipment is
safe. Hollis says this is simply not the case: No
matter how vigilant inspection and maintenance
may be, you can’t count on old equipment to behave
the way it did when it was new. While there’s no
way to prevent 100
percent of incidents
involving older
pipelines, taking a
proactive approach
to maintenance
and upgrading equipment to comply with evolving
industry standards will cut down the number of
incidents dramatically.
SCENARIO 2
A TRIP TO THE CIRCUS: PAYING ATTENTION
TO PEOPLE AND PROTOCOLS
Most occupational injuries are usually triggered
by an individual worker’s unsafe work practices
and they are the one to suffer the consequence:
lacerations, slip, trips, and falls, repetitive motion,
etc. In theory, it should be easy to avoid most
occupational safety hazards: You establish rules and
protocols, and your people follow them – but things
aren’t always that simple.
Think about the circus: Sometimes, despite the
posted warnings, people still test the patience of the
performing bears. This is also true for employees
following protocols. Say you have a particular safety
protocol in place: All personnel must wear a protective
facemask to perform “Task A.” So far, so good.
But it turns out that the masks provided,
although up to code, don’t offer the visibility
required to complete the assigned task. Workers
repeatedly bring the problem to the attention of
a supervisor, but it’s considered “low-priority,” so
nothing gets done. Eventually, fed up with getting
nowhere and still needing to meet quotas, workers
just stop wearing the masks – and then a chemical
spill sends a dozen maskless workers to the hospital.
So, What Can You Do?
Bring It Down To The Human Level.
At the end of the day, what’s really important is how
efficiently you get feedback from the personnel in
the field, and how effectively you act to solve their
problems via proper supervision. Hollis says that
while cutting-edge computer programs are well and
good, the best solutions don’t have to be complicated
or high-tech. Sometimes, less really is more.
“Safety is not the
absence of incidents,”
says Barry Hollis, “but
rather the strength of
your defenses.”
CONTINUED ON PAGE 26