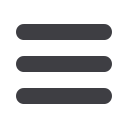
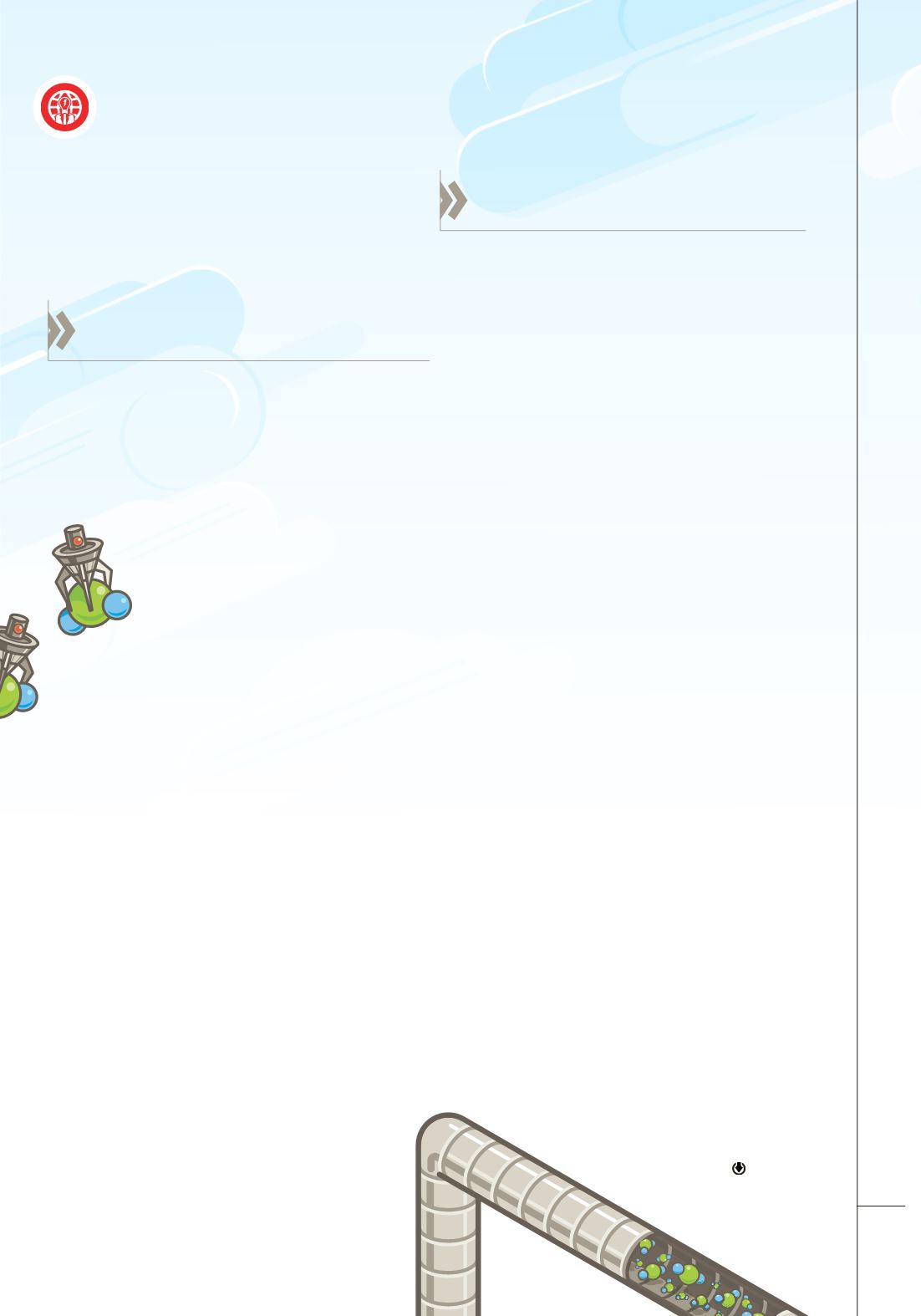
27
I N N O V AT I O N S • V O L . V I I , N O. 1 • 2 0 1 5
Future Thinking
CONTINUED FROM PAGE 11
international conference on carbon capture. “This
type of injection of water, brine, and gases has been
done for many decades.”
And although there are several possible methods
out there for capturing CO2, most in the industry
agree that there’s really only one transportation
method that makes sense: pipeline.
Opportunities on the Horizon
Mike Kirkwood, Ph.D., is Director of Transmission
Market Development for T.D. Williamson (TDW),
which has experience cleaning and inspecting
pipelines carrying naturally occurring CO2 to
production wells for enhanced oil recovery. Kirkwood
says pipeline is an optimal choice for moving
compressed CO2 to storage sites because
pipelines have a strong safety record, and
existing pipeline technology – such as
specialized welding and valve installation
techniques – can be leveraged with new
and repurposed CCS pipelines.
But Kirkwood is quick to point out
that pipeline transportation isn’t without
challenges. Hot tapping a CO2 line, for instance,
will require special care. CO2 is sensitive to
temperature and pressure changes, and slight
fluctuations – common during a hot tap or cleaning
operation – could trigger a phase change from
gas to liquid or solid, essentially creating dry ice
that could damage or block the pipeline. Another
challenge is that many pipeline inspection tools
contain urethane components. Urethane is a popular
choice because it offers elasticity and is abrasion-
resistant. But urethane naturally absorbs CO2, a
problem that under certain circumstances, such as a
change in pressure, could cause the urethane to burst.
Because of this, Kirkwood says, a number of inline
inspection tools will need to be re-designed or special
procedures developed.
And finally, there’s the issue of corrosion.
Although carbon steel pipelines are considered
the most durable and affordable option for CCS
transportation, they are also highly susceptible
to corrosion – and carbon-captured CO2
is corrosive by nature and, combined with
the other impurities, can make for a heady
corrosive mix.
The result? “You’re probably going to have to
inspect more,” Kirkwood says. “It comes back to what
the service companies are going to do to help the
operators manage and operate these pipeline systems.”
Building Momentum
As of February 2014, there were 21 large-scale CCS
projects in operation or construction globally, the
CCSA reports. In Norway, the long-running Sleipner
project – widely credited with being one of the first
CCS projects of its kind – is still underway. Since it
started operating in 1996, the Sleipner project “has
captured nearly 1 million tons of CO2 every year
from gas production and injected it into a deep saline
formation under the North Sea,” says Warren.
In the United Kingdom, the upcoming White
Rose project will capture CO2 from a coal/biomass
facility, while a similar project called Peterhead will
capture CO2 from a fossil gas power plant.
And in October 2014, Canada’s SaskPower
added a CCS facility to its Boundary Dam power
plant in Saskatchewan. The project is projected to
reduce carbon emissions from the coal-fired plant by
90 percent.
“SaskPower has made significant progress in
making a valuable contribution to demonstrating a
viable technical, environmental and economic case
for the application of CCS to power plants,” Warren
says, adding that he hopes projects like Boundary
Dam will provide momentum for similar projects
around the world.
Further, the CCSA has reported, a number of
regions are looking to develop pipeline networks that
will enable cost effective harvesting of CO2 emissions
from multiple sources. The White Rose project in the
UK, for example, will include the “Yorkshire Humber
CCS Trunkline,” a pipeline able to carry a large
amount of CO2 from power and industrial emitters.
Similar pipeline projects are being developed in
Alberta and Australia.
Someday, you may be able to walk into a
convenience store to buy a bottle of something
that resembles the fictional EV-EON. But until
then, innovators around the world, representing
a wide range of industries, are working to make
CCS technology a practical and safe way to
reduce CO2 emissions and protect the
Earth from the damaging effects of
climate change.