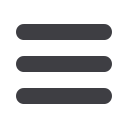
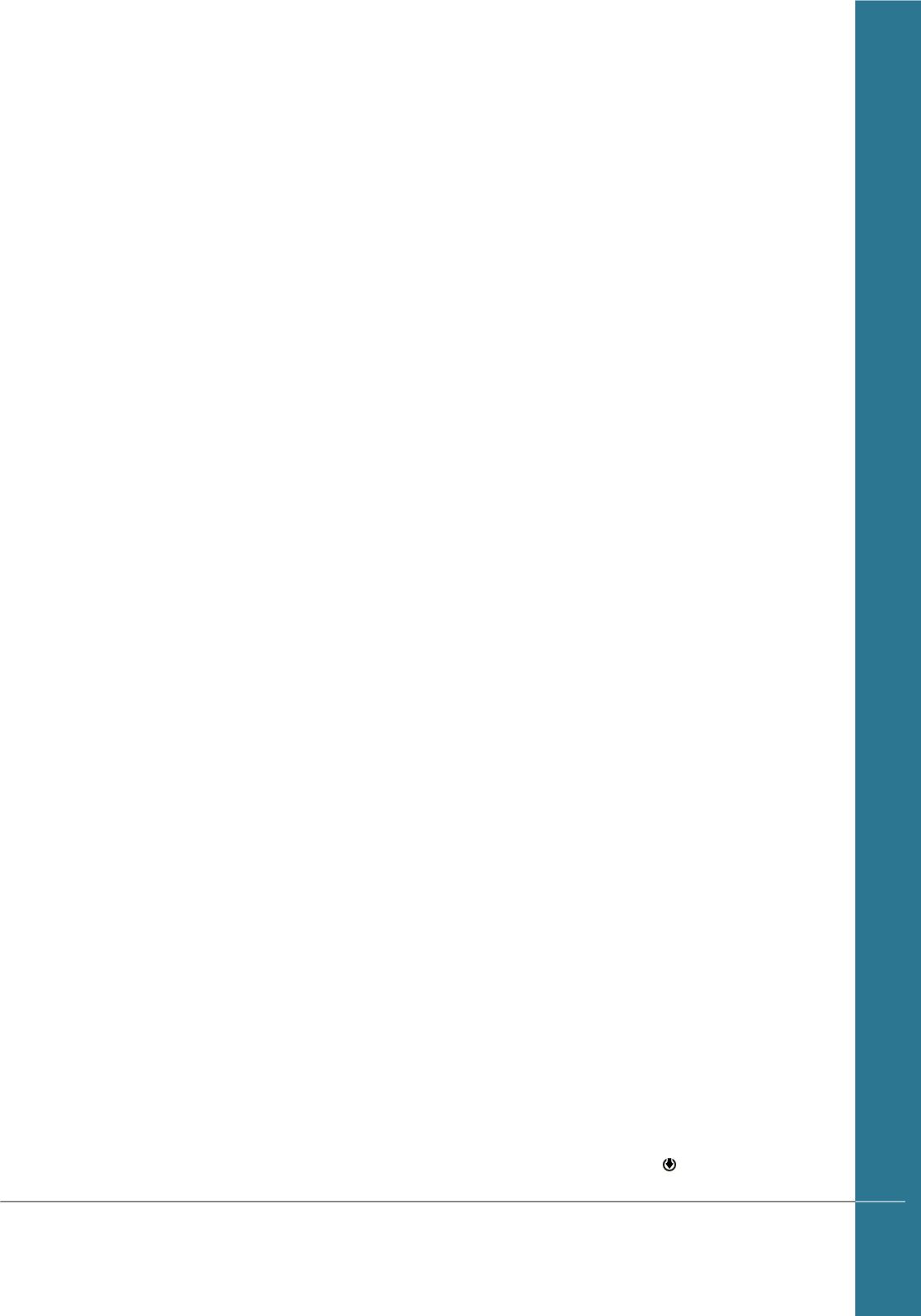
drones. And those aren’t always positive,
are they? We’re actually about aviation that
flies robots.”
Ears Underground:
Intelligent Listening
If dogs depend on smell and UAVs on sight, it
only stands to reason that another innovation in
pipeline damage detection would rely on sound.
Through its Distributed Acoustic Sensing
(DAS) technology (i.e., fiber optics), UK-
headquartered OptaSense puts what it calls “a
pair of ears” every 10m (about 32 feet) along the
pipeline to monitor third-party activity that has
the potential to cause damage, including people,
rock fall, or moving vehicles. According to Dr.
Chris Minto, OptaSense Operations Director,
DAS can provide instant detection of an event, its
location, and its classification.
As an example of the technology’s capabilities,
Minto says, “We can detect a pilferage party
trying to dig down to a pipe and allow enough
warning to enable a responder to get there before
the pipe is breached.”
The company recently extended what it calls
the power of sensing to the Internet, introducing
mobile device applications that use the DAS
sensor to place the owner “right in the action.”
“Imagine the guiding hand on the right of way
telling you which way to go to get to the event
you are interested in,” Minto explains. “Cell
phone and tablet applications have their place,
but communications reach-back is essential,
together with a controlled method of confirming
location. This helps in many places where
directions and mile markers may be vague.”
The Inside Track: Inline Inspection
Can Prevent Catastrophes
TDW’s Jeff Foote agrees that “unique and creative”
ways to identify pipeline damage are part of a
holistic approach to integrity assessment and
management. But he cautions that sniffing dogs,
overhead surveillance, and fiber optics aren’t a
replacement for having a good inline inspection
(ILI) program to detect cracks, deformations, and
other defects – problems that could turn into
catastrophes with just some pressure cycling.
“Inline inspection is a critical part of the set of
things operators have to do to maintain integrity,”
he says. “It’s also a first line of defense, in that
ILI can uncover dents, gouges and other damage
before they have a chance to worsen into leaks
or ruptures.”
“The dent that no one knows about might not
seem like an immediate threat,” says Foote. “But
it also may not take much for it to become a
leak that’s environmentally severe or pipe break
that results in explosion and major public safety
consequence.”
Among the tools available to TDW clients
are Deformation (DEF) and Geometry (LGT)
measurement inspection tools to identify dents,
and magnetic flux leakage (MFL) inspection
to identify gouges with metal loss typical of
inadvertent backhoe contact.
“We also offer a low field magnetic (LFM)
inspection technology that will find local changes
in metal property around the perimeter of a pipe
dent,” says Foote. “This is critically important
to preventing the possible crack formation and
fatigue failure at the location of a pipe dent that
re-rounds when operating pressure is applied.”
With a combination of these inspection
methods and comprehensive analysis, TDW
can provide dent prioritization reports that
are highly useful to an operator’s overall risk
assessment program.
In a perfect world, Foote suggests, third-party
damage would be eliminated through prevention.
And operators are making efforts toward that
ideal: think warning signs, line markers, perimeter
security, blast and wheel load calculations, and, in
the United States, the federally mandated ‘8-1-1
Call Before You Dig’ awareness campaign.
Yet damage to pipelines from third-parties
continues to happen in the real world.
So until Foote’s ambition is achieved, the
industry will continue to leverage all of the
pieces of the integrity puzzle. Dogs will keep
sniffing, drones will keep watching, microphones
will listen, and intelligent inline inspection will
remain a smart way to uncover anomalies before
they become consequential.
I N N O V AT I O N S • V O L . V I I , N O. 1 • 2 0 1 5
F E AT U R E S T O R Y
25