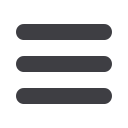
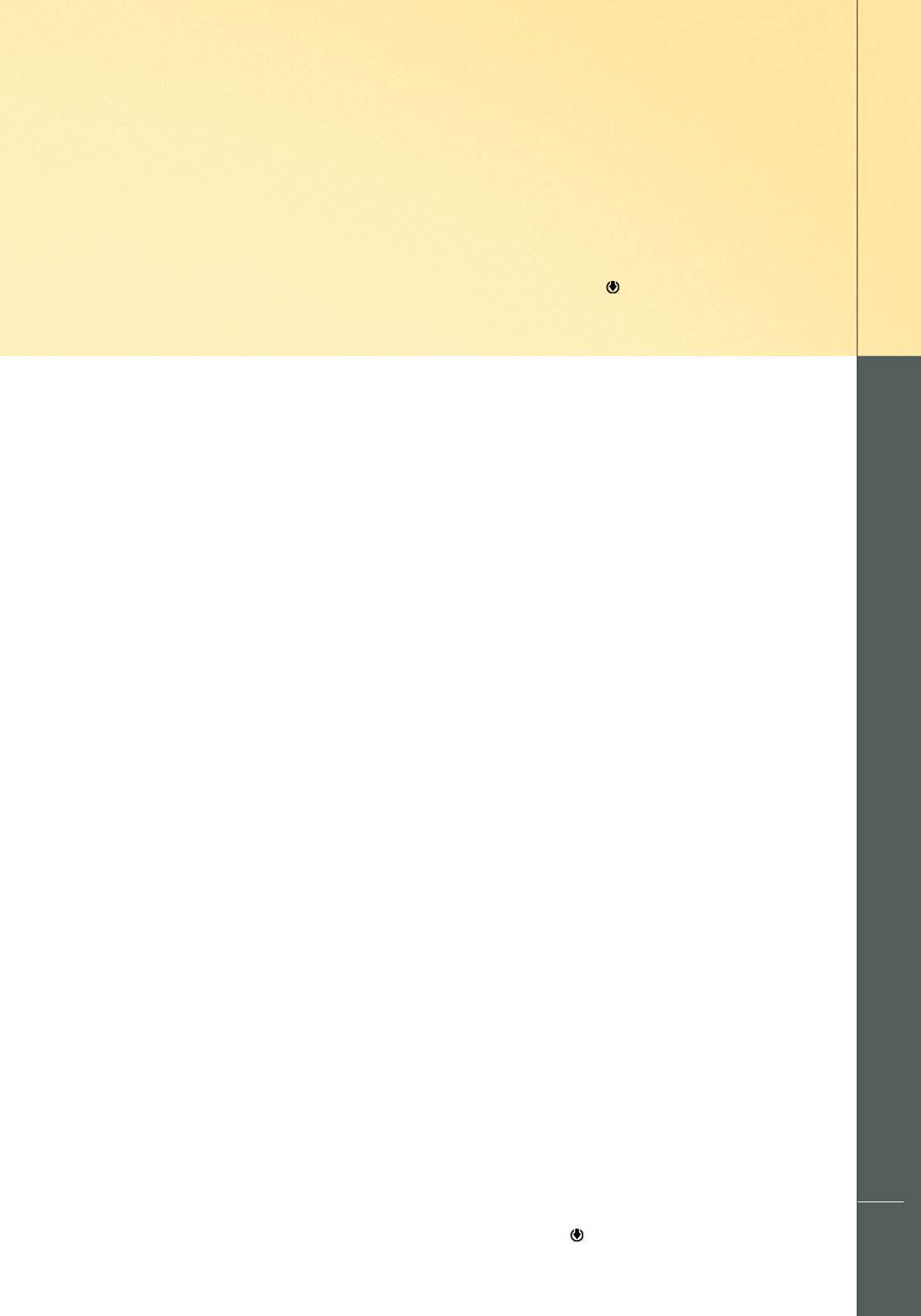
27
I N N O V AT I O N S • V O L . V I I , N O. 2 • 2 0 1 5
how to go about protecting pipeline integrity.
Instead of presenting operators with a lengthy list
of “do’s and don’ts” to prevent pipeline failure,
more governments are asking, “Show me what
you’re doing to protect your pipelines’ integrity.”
The result has been greater levels of innovation
and growing appreciation for the many benefits
of PIMS.
This trend is encouraging. The practice of
well-crafted PIMS processes – with the assistance
of carefully chosen software solutions – is proving
to be an added-value proposition for pipeline
operators. Every bit of accurate, aligned data
that operators cull from their PIMS processes
equips them to make better choices, choices
that ultimately help them achieve their mission-
critical goals of greater pipeline safety and
increased efficiency.
of midstream and gathering lines is the fuel cost to
gather, dehydrate, and compress the gas,” Zellou
explains. “Not only does efficient liquids removal
create a revenue opportunity, it also helps the
operator minimize costs.
“Operators already know this simple equation:
profit equals revenue minus cost,” he adds.
“Using technology to generate additional revenue
and control costs makes shale development
less sensitive to price swings and increases
profitability.”
So, where, exactly, does automation figure into
the calculation? For Zellou, it fits into both the
health and wealth of a pipeline. And the potential
impact is enormous.
Although he’s still working to put hard
numbers to the benefits Eagle Ford operators
might accrue by, for example, switching to
automated pig launching – using equipment that
can be remotely programmed to deploy multiple
spheres or pigs on a regular schedule – the
preliminary figures suggest savings in the hundreds
of thousands of dollars.
And here’s how that adds up: Not only can
automated systems more efficiently launch spheres
to capture valuable NGLs and optimize product
flow (that’s the wealth part Zellou mentioned),
they can dispatch cleaning pigs to eliminate
paraffin, the wax that creates an environment
where corrosion-causing, deadly H2S-breeding
microbes thrive (which is the health part).
Automation can also reduce the blowdown
associated with opening and closing the doors
during a normal pigging operation by up to 90
percent. And it increases the life of the valves used
in the system because they’re operated less.
But beyond those benefits, automated,
unmanned operation reduces work hours and
helps protect personnel safety. And in the Eagle
Ford, the well-being of the workforce has become
a significant challenge.
That’s because as the region has boomed, travel
along the Eagle Ford’s remote, narrow roads has
become more treacherous. Crews who need to
load and retrieve pigs or spheres from a non-
automated pigging system may face daily trips to
those lines, easily driving as much as seven hours.
But with auto-launching, field personnel are on-
site only twice during an entire cycle of a week or
more, significantly reducing personnel travel time.
Are Lower Prices the NewNorm?
It could be said that for oil and gas operators, there’s
no such thing as living in the present. Even the
commodity pricing structure is built on futures.
So, what do the years ahead hold for the
Eagle Ford? What will the new normal be? Given
the complexity of the global energy market, the
impulses of OPEC, and the continuing ban on
American crude exports, it’s not easy to predict
with complete certainty.
But what we do know is this: Automation is
continuing to breathe new life, health, and wealth
into the region.
TheEconomics of Efficiency
CONTINUED FROM COVER STORY PAGE 19