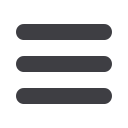
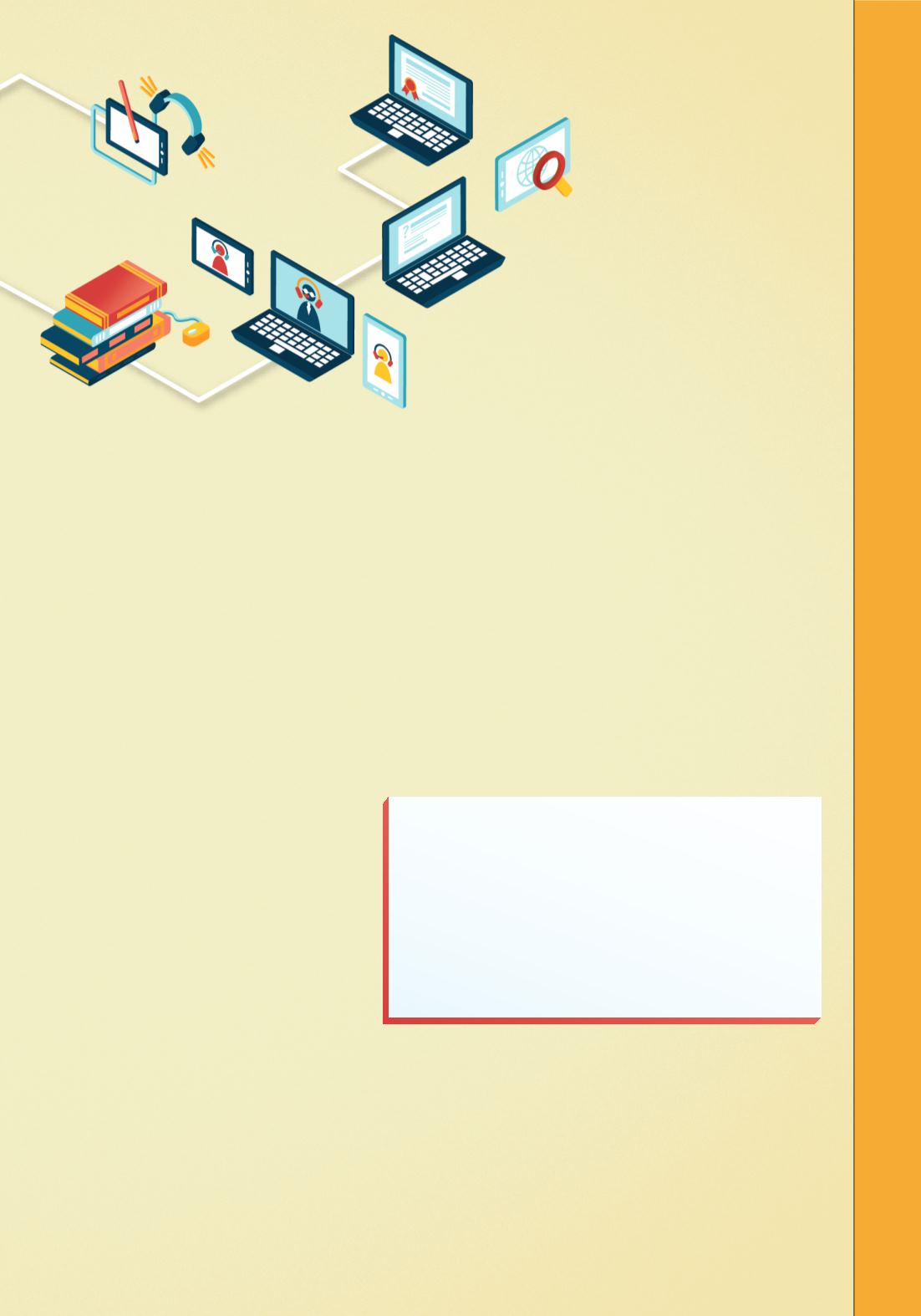
F E AT U R E S T O R Y
I N N O V AT I O N S • V O L . V I I , N O. 2 • 2 0 1 5
25
PIMS processes easily accessible to everyone
concerned, but also helps with the tremendously
important process of analyzing and fully
leveraging the information that you gather.
Does one area of pipeline require more repairs
than others? Has one section of pipeline been
more prone to corrosion? PIMSS can help you
recognize these trends and map out a plan for
addressing them.
And PIMSS technology is continuously growing
and evolving, so even more valuable options have
been recently introduced and more are on the
way. One recent development is the arrival of
cloud-based data storage, which provides another
convenient option for accessing and
backing up pipeline data. Another new
trend: Mobile options that allow operators
to carry out PIMS-related tasks from their
hand-held devices. The technology is
similar to consumer products that allow
people to start their car from inside their
home on a cold day. A mobile-based
PIMSS program might even allow you to
ask the system to evaluate a new data set
while you’re on the way to the office.
But Kirkwood cautions users not to get
too dazzled by PIMSS technology too quickly.
Before purchasing a system, it’s critical to
understand exactly what you’re buying, and
what it is and isn’t capable of doing. PIMSS, for
instance, provides helpful “snapshots” of the
condition of your pipelines,
but the current technology
does not harness the concepts
of “big data” that can be
analyzed to identify greater
patterns or trends.
Accurate and Aligned:
Getting the Whole Picture
To get the most out of PIMSS technology, and
PIMS management in general, operators should
not only be collecting data, but also taking steps
to ensure they’re getting accurate, aligned data. In
other words, all of the pieces of the puzzle should
make sense when put together, showing exactly
what is happening within the pipeline system.
In most cases, alignment requires extra effort,
because the information operators gather about
their pipeline systems is typically pulled from
multiple sources. Putting everything together for
a big-picture look at the pipeline, its risks, and
the best measures for managing it can get a bit
tricky. And whenever companies need assistance
in this area, specialized service providers, like T.D.
Williamson, are available to guide them.
“Imagine having two pieces of see-through
paper,” Kirkwood says. “On one piece, I’ve got
the pipeline, and on the other piece of paper, I’ve
got the defects. I’m putting one on top of the
other, and I’m trying to overlay where all of the
defects are on my pipeline. However, the problem
is the pieces of paper are two different sizes, so the
It’s a complicated, multistep process,
and it can be a bit daunting for operators,
but the
payoffs in terms of
safety, efficiency, & financial
return
are well worth the learning curve.