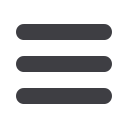
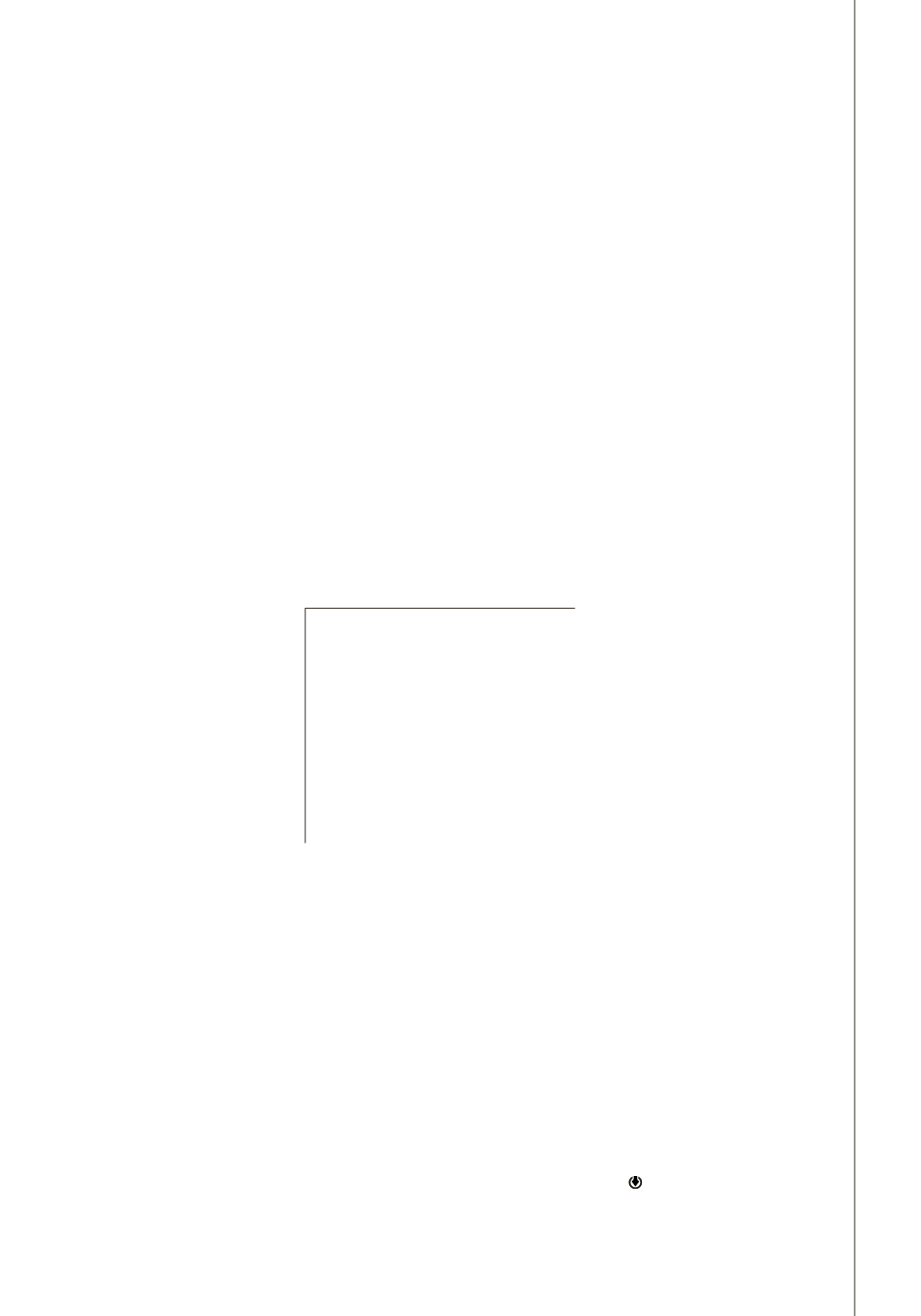
I N N O V AT I O N S • O C T O B E R -
D E C E M B E R 2 0 1 4
7
With a figure that steep, it’s easy to understand
why detecting, monitoring, and mitigating motion-
induced strain events have become an increasingly
high-profile, high-tech part of integrity management
— so much so, in fact, that two organizations have
recently sponsored Joint Industry Projects, or JIPs,
around the topic.
JIPs Encourage Detection And
Validation Of Strain-Based Events
A JIP is a way of creating knowledge in partnership,
looking for a solution to a specific problem that
requires fundamental or applied research. In the
United States, both the Virginia-based Pipeline
Research Council International (PRCI) and the
Center for Reliable Energy Systems (CRES), Dublin,
Ohio, have within the last few years organized JIPs to
help the pipeline industry understand how detecting
and validating the effects of ground movement strain
can aid in reaching pipeline integrity goals.
While a fair amount of PRCI’s work has
focused on strain-based
design for the construction
of new pipelines, the CRES
collaboration turned its
attention more to technology
deployment for assessing strain
events in existing pipelines.
CRES’ JIP group, which
included Kinder Morgan,
Spectra, T.D. Williamson, and
other operators, inspection
companies, and experts in
geotechnical science, materials,
welding, and mechanics, set about to identify:
�
The chief geotechnical hazards causing
strain events.
�
Inspection tools to detect related
pipeline damage.
�
Material properties and flaw
characteristics that increase the likelihood
of damage from pipeline movement.
�
Mitigation and monitoring activities.
CRES’ JIP findings were presented at the
Government/Industry Pipeline R&D Forum
sponsored by PHMSA in July 2012. The group
reported that even sophisticated strain capacity models
left something to be desired in terms of precision.
Among the group’s concerns, for example, was the
fact that the strain capacity tests were developed under
laboratory conditions. As such, the models measured
strain on straight, undamaged pipes, without taking
into account interacting defects, field bends, or load
differences that could occur on site.
The JIP suggested that to more accurately
determine the effects of ground movement events
on in-service pipelines, operators would need to fill
in missing data about material properties and flaw
characteristics; understand how longitudinal strains
interact with anomalies from corrosion or mechanical
damage; and employ better means of detecting and
monitoring flaws and fittings.
Moving Toward Better, More
Complete Information
Jed Ludlow, principal inline inspection (ILI) data
scientist for T.D. Williamson, applauds the JIP’s
work as part of the evolution helping to better
predict fitness-for-service in pipelines subjected to
ground movement. He also sees
advances in ILI technology as
further evidence of progress in
the right direction.
“For many years, in the
case of strain events, pipeline
operators had to rely on data
that was gathered from outside
the pipe, above ground, to
make integrity management
decisions,” Ludlow says. “That
meant there was no way to
really examine the entire length
or surface of the pipeline for anomalies. But
today, instead of relying on external data about
ground motion and wondering if the pipeline has
been affected, we can use sophisticated ILI to
examine every square inch of the pipeline, from
start to finish, using non-destructive evaluation
(NDE) techniques.
“For example, specific to strain events, by
running XYZ mapping tools and performing a
bending strain analysis, the operator now has a
complete picture of a pipe segment’s centerline
shape from end-to-end,” Ludlow explains.
And most operators will agree that this is
a groundbreaking step toward more complete
integrity management.
Although ground
movement causes less
than 10% of pipeline
incidents in the US
and Europe, the annual
associated costs figure
in the millions.