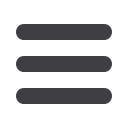
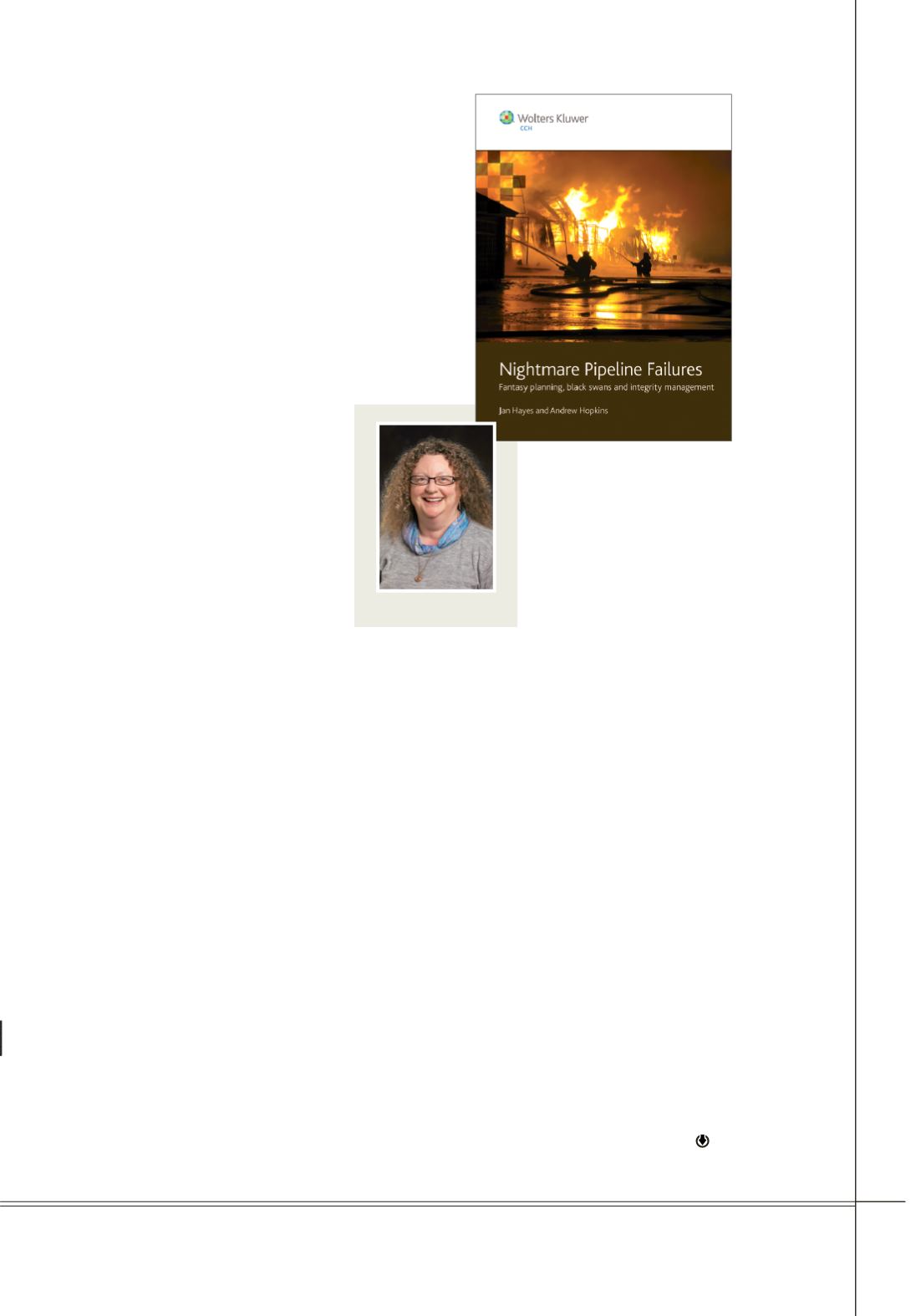
process that happens so far below the surface
that operators aren’t even conscious of it. The
real culprit, she explains, is a lack of “safety
imagination”: Because most operators have never
experienced a disaster, they can’t imagine a disaster
actually happening.
Look at almost any major oil spill or gas leak,
Hayes says, and you’ll see the same pattern: There
was evidence, but nobody really believed it. Hayes
recalls experiencing a similar sense of disbelief
during her early career as a process engineer with a
major oil and gas company: She was
shocked when the North Sea Piper
Alpha oil platform accident claimed
the lives of more than 160 people.
“I just didn’t think things like
that could happen,” she says. “It’s
easy to have the mindset of, ‘It can’t
happen here because I’ve never seen
it happen here’ – but there’s always
the potential. Safety imagination is
about knowing in the back of your
mind that things can go wrong.”
But how do you encourage
employees to develop – and use – their safety
imagination when it comes to pipeline integrity?
How do you convince them to report anything
that seems suspicious, even if they’re fairly certain
it’s nothing major?
It’s a challenge, Hayes says. But with the right
cultural shifts, it’s not impossible.
The Benefits of “Chronic Unease”
Some safety experts and researchers use the term
“chronic unease” to describe the ideal approach
to safety. It’s the opposite of the “it can’t happen
here” mindset; an outlook that remains aware that
something could go wrong at any time. Chronic
unease means having specific, customized plans in
place for each type of accident; it means thinking
proactively about public safety rather than
focusing solely on compliance.
It also means encouraging people at all
levels of a company – from junior engineers
to maintenance people to C-level executives
– to think critically about safety. Some
organizations are accomplishing this by creating
specialized safety workshops aimed directly
at groups like executives and board members.
Others enact bonus systems that tie financial
rewards to process safety. The most important
thing to do, though, is to create a culture where
everyone feels empowered to speak up when they
notice something unusual – even if it turns out to
be nothing.
“We always hear about the guy who noticed
something and reported it, and if it wasn’t for him
there would have been a huge disaster,” Hayes
says. “That’s all well and good, but we also need
to hear about the guy who thought there was a
problem and reported it, and it turned out that
everything was fine. That guy should still be
congratulated – because it’s not about whether he
prevented a catastrophe. It’s about the fact that we
need those reports to be made.”
I N N O V AT I O N S • V O L . V I I , N O. 3 • 2 0 1 5
9
Some of the research on which this article draws was funded by the Energy Pipelines Cooperative Research Centre, supported through the Australian
Government’s Cooperative Research Centres Program. The cash and in-kind support from the Australian Pipeline Industry Association Research and
Standards Committee is gratefully acknowledged.
“We also need to hear
about the guy who
thought there was a
problem and reported
it, and it turned out that
everything was fine.”
Dr. Jan Hayes